Gas Activated Systems
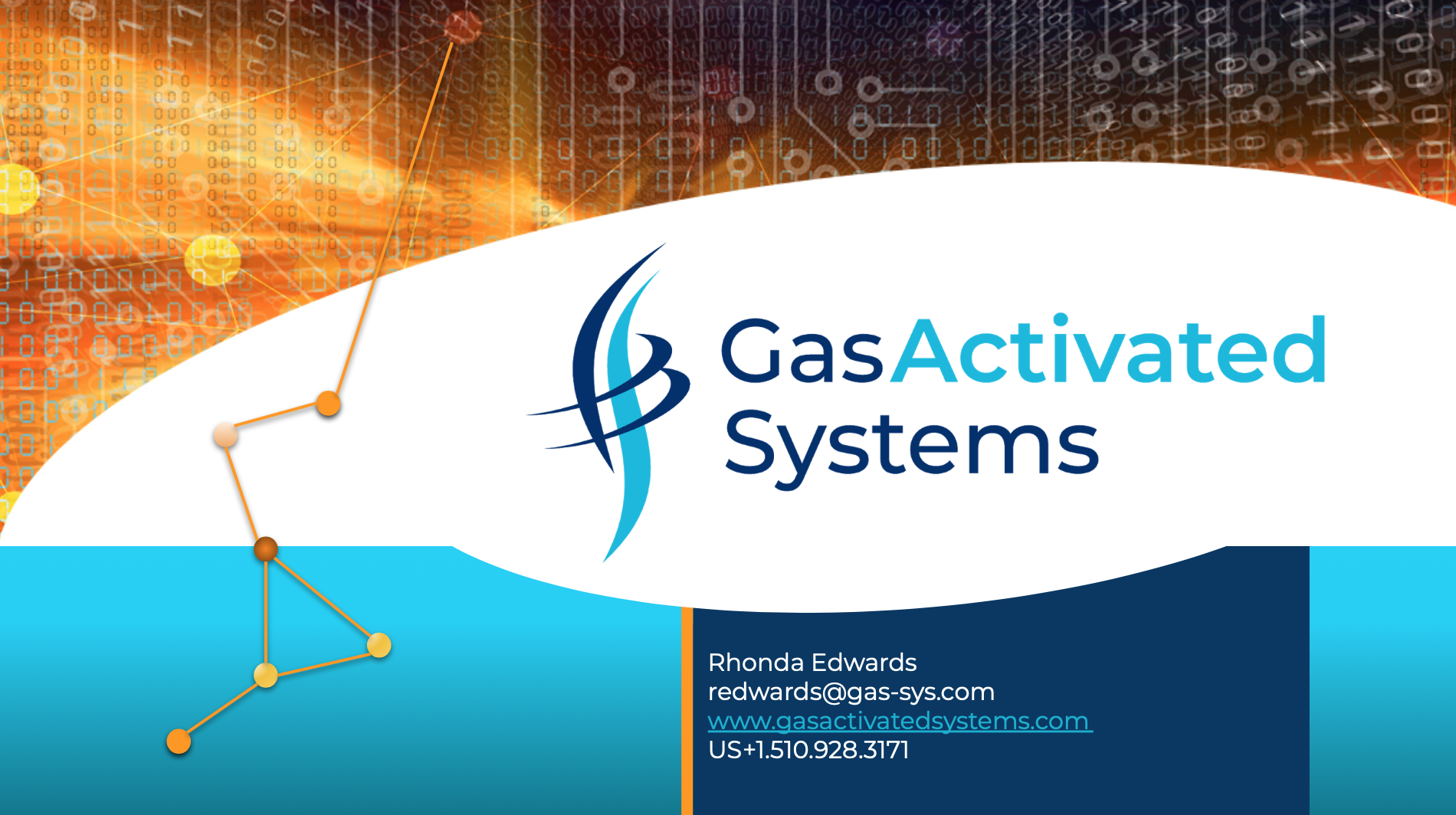
Using its advanced Industrial Internet of Things infrastructure that includes state-of-the-art sensor technologies, Gas Activated Systems delivers proven solutions to the industry. Local, adaptive mesh communications, self-repairing long-range wireless and the backhaul to the cloud to monitor and control fugitive gas emissions at oil and gas exploration and production sites, refineries, storage and transmission facilities. Through this system, gas emissions are, mapped and analyzed 24/7 in real-time, providing the intelligence necessary for immediate control, as well as, collection and analysis of large historical data sets of methane and other explosive and combustible emission sources.
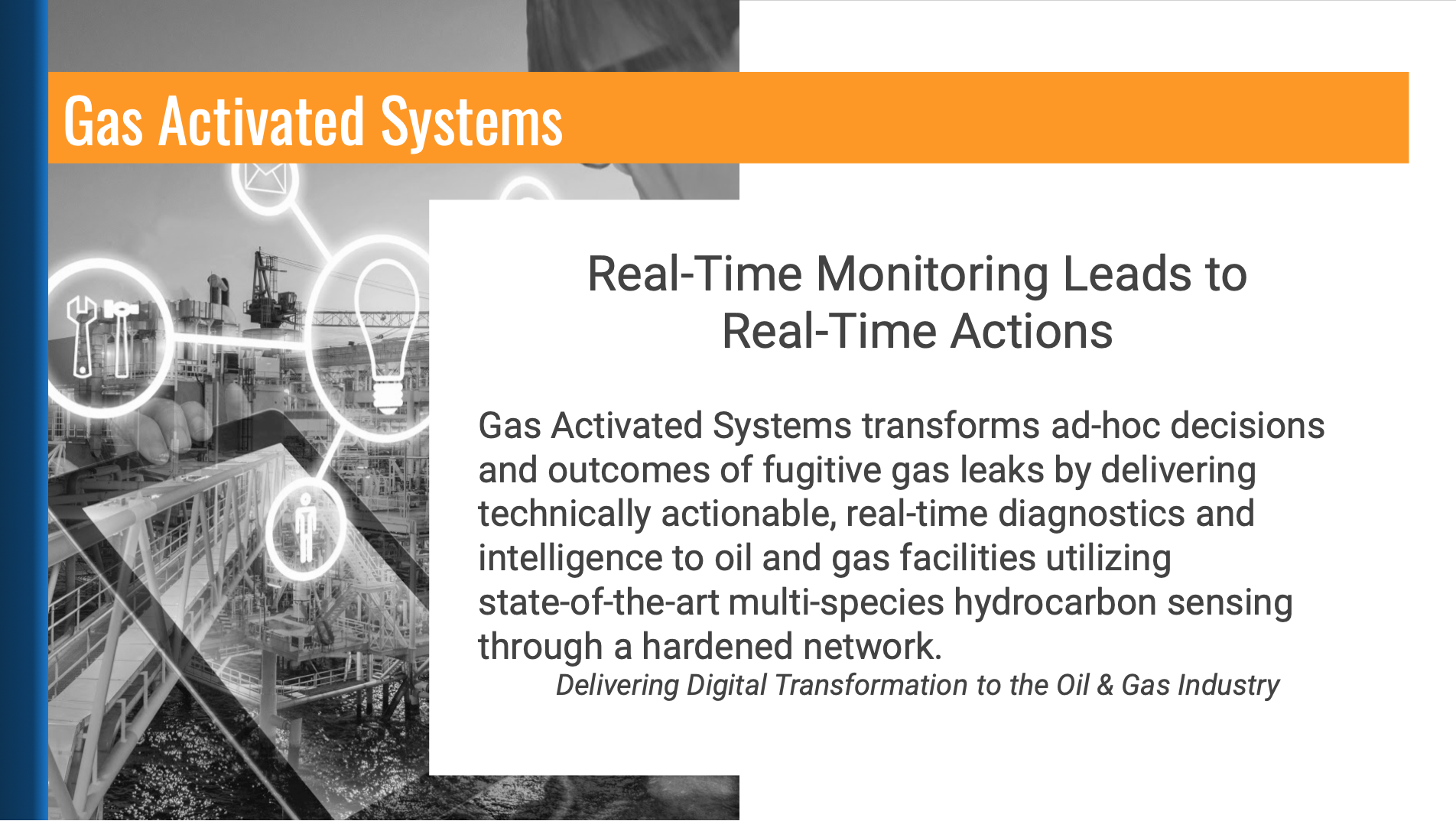
Hydrocarbon Emissions are a problem for the entire world, having a growing effect on our planet. Within the oil & gas industry, the issues affect the bottom line. We’ve been working with a number of influencers in the Permian Basin area, through our work at Texas Tech University. Dr. Bradley Ewing, Professor of Energy Commerce and Dr. Marshall Watson, Professor of Petroleum Engineering share with us that these accidents are happening if not every day, at least every week in Permian. The issue is not just the 3 hours it will take to get personnel to the burn center, and it’s not just the valuable piece of equipment that was destroyed, but moreover, it’s the loss of revenue as it has shutdown production of the valuable payload they could be extracting from the ground.
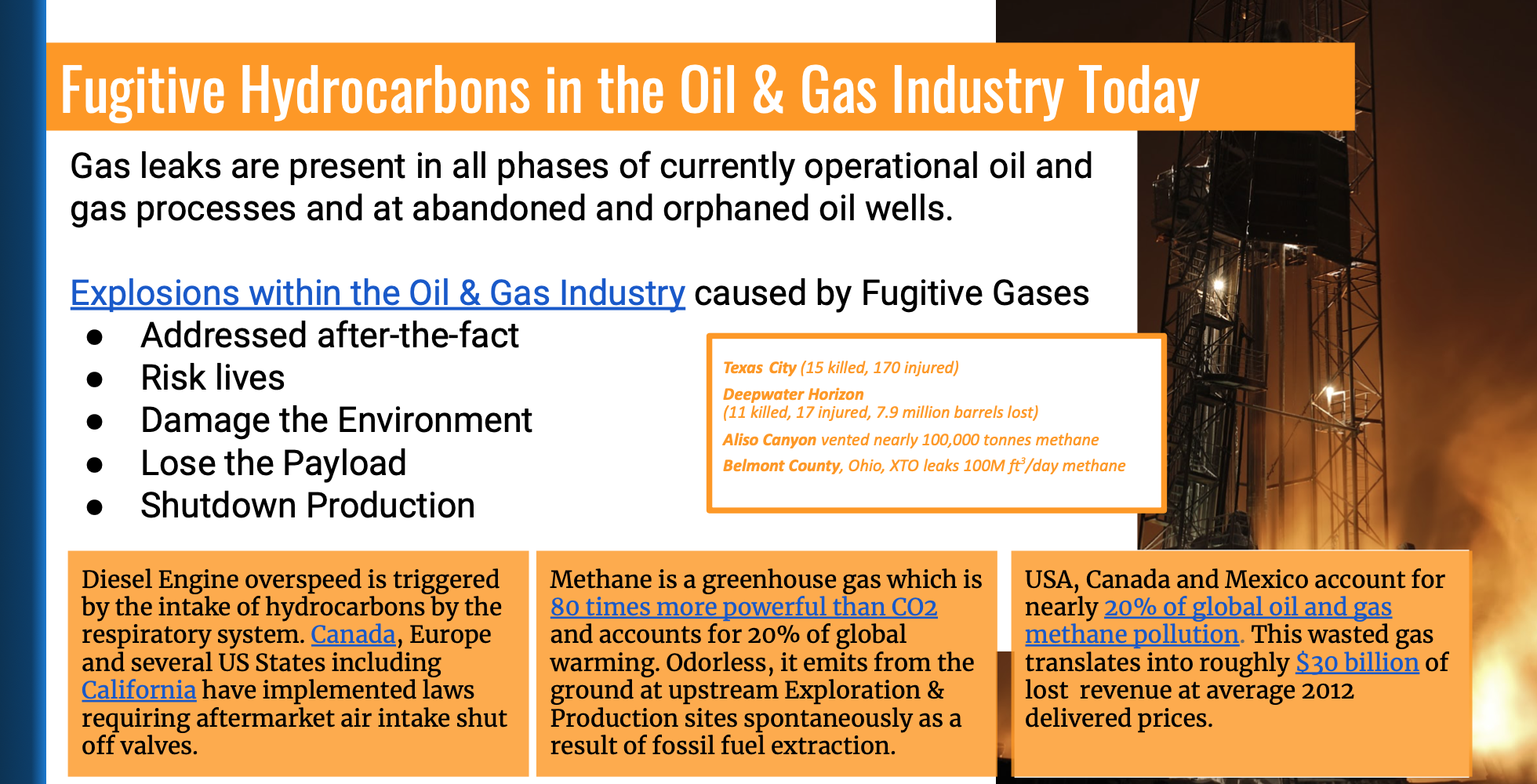
Numerous catastrophic events have resulted in injuries, loss of lives, loss of equipment and resources as well as causing significant environmental damage. The most infamous of these was the Deepwater Horizon incident that began with the uncontrolled release of hydrocarbons from the wellhead. Preventing engine runaway events by the use of overspeed protection devices is recommended by OSHA and is now required in Canada CSA-B622 , Europe EN 1834 and several U.S. states including California.
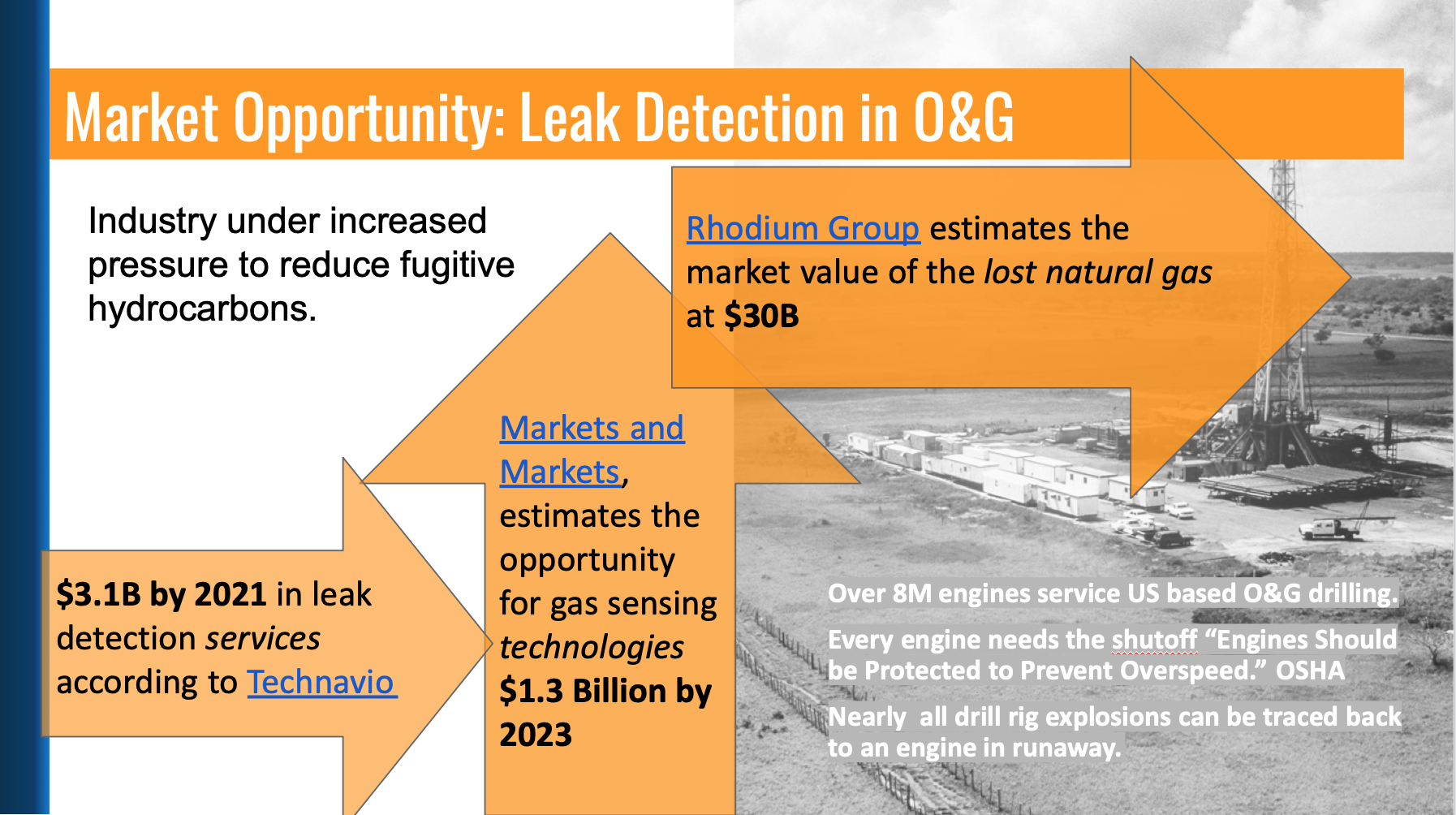
We are introducing a new technology. This sensor brings to the world for the first time ever, the ability to sense EVERY HYDROCARBON species in a single sensor.
Because 1 in every 2,500 untested instruments will fail to respond to a dangerous concentration of gas, many large businesses use a test/calibration station for bump tests and manually calibrate their gas single-gas detectors daily.
This new MEMs technology uses micro-fabrication techniques. These enable multiple functional units to be integrated on a single chip, thereby making possible such concepts as lab-on-chip (LoC).
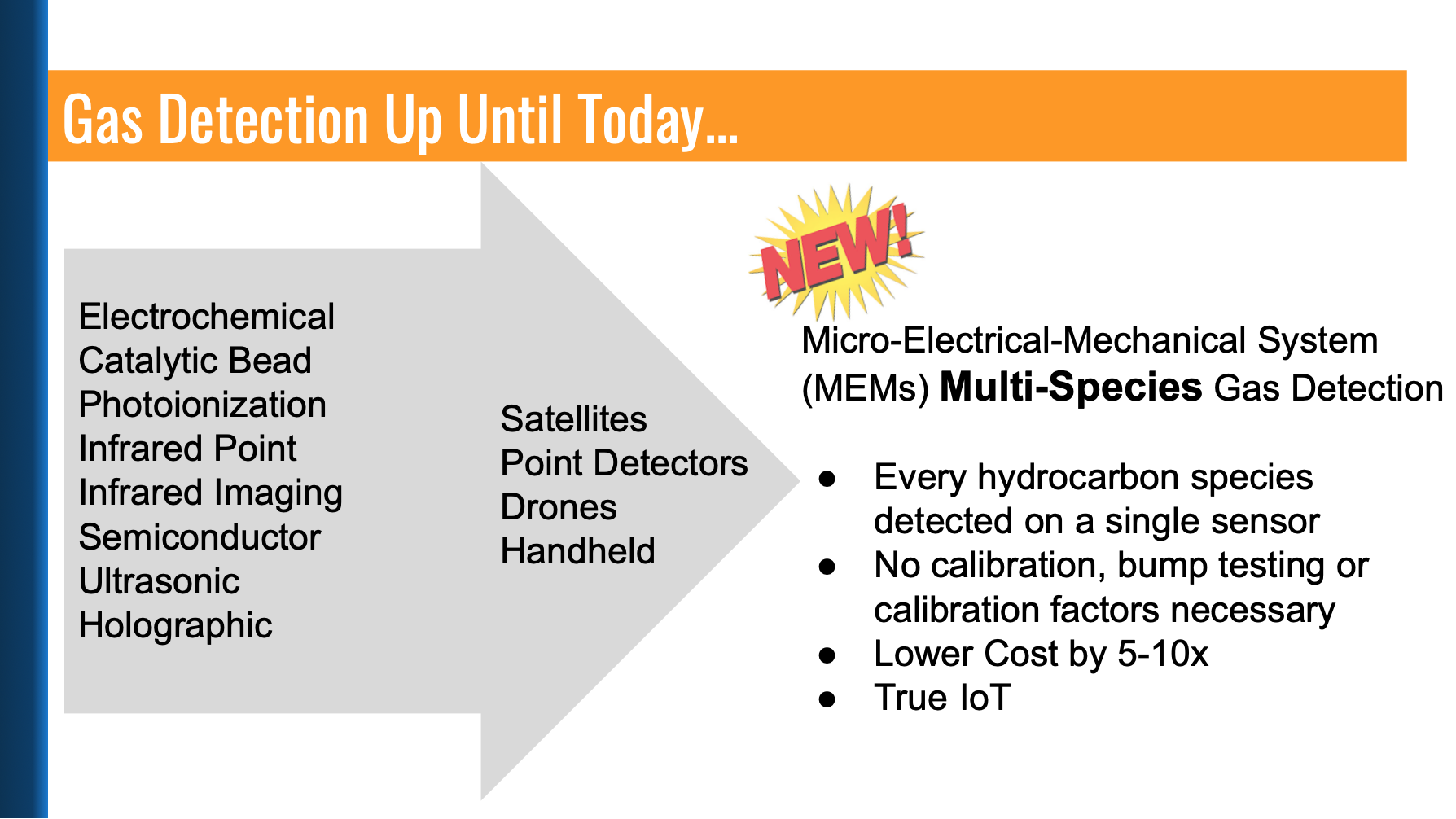
GAS DetectSys™, a state-of-the-art MEMS-based, sensor system, is a product of over a decade of development time and millions of dollars in development costs. It measures flammable gas levels with speed and accuracy not found in other sensor systems. Advanced sensor technology and sophisticated analysis software allows for the rapid detection, identification and quantification of a wide variety of gases.These sensors are able to identify and quantify multiple flammable gases on a single chip complete with accurate Lower Explosive Limit (LEL) determination. The system provides geolocation, and long range wireless connectivity. Sensors can be deployed on fixed, mobile, and ancillary assets. Broad-based deployment becomes feasible by dramatically lowering the footprint utilizing a silicon lab-on-a-chip sensor. With its silicon cost-structure,large scale sensor deployment becomes feasible.
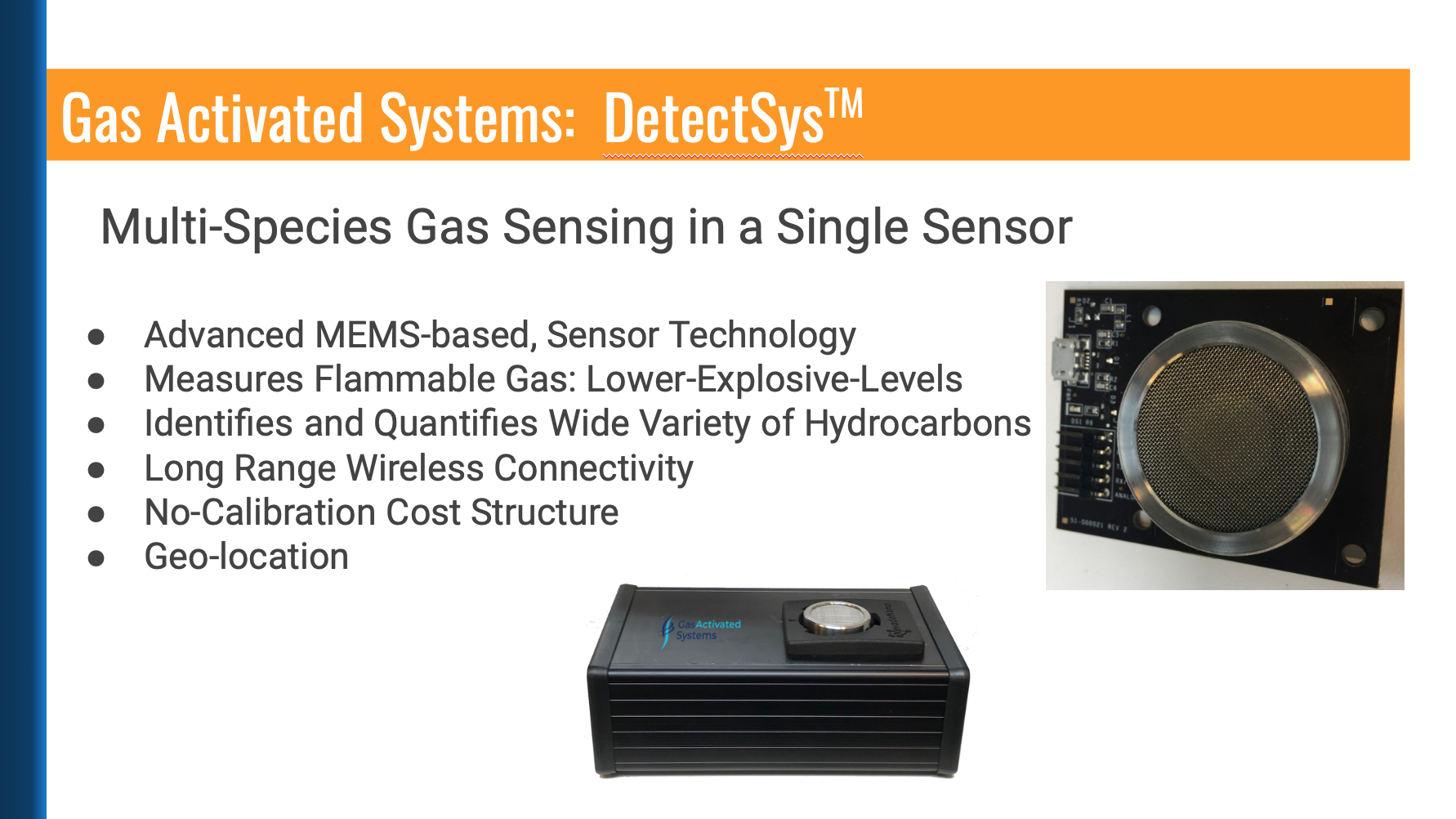
GAS PreventSys™ is a patented Industrial Internet of Things (IIoT) platform that gathers data from multiple sources to map a broad spectrum of explosive and combustible gases in real-time and real-space. This technology allows the autonomous, global, wireless networking of an unlimited number of sensors and the split-second analyses of data. Subsequent action both in the sensor mesh network and in the cloud are designed to prevent catastrophic events, saving lives, valuable resources and assets. Historical big data sets can be mined and analyzed using artificial intelligence to enable data-driven decision making for all aspects of site control, cause and effect relationship extraction, and disaster prevention in comprehensive ways not previously possible. Utilizing Thread technology, the mesh infrastructure simply adds and removes nodes to its self-healing network; redesignating gateway-to-node relationships autonomously as needs require.
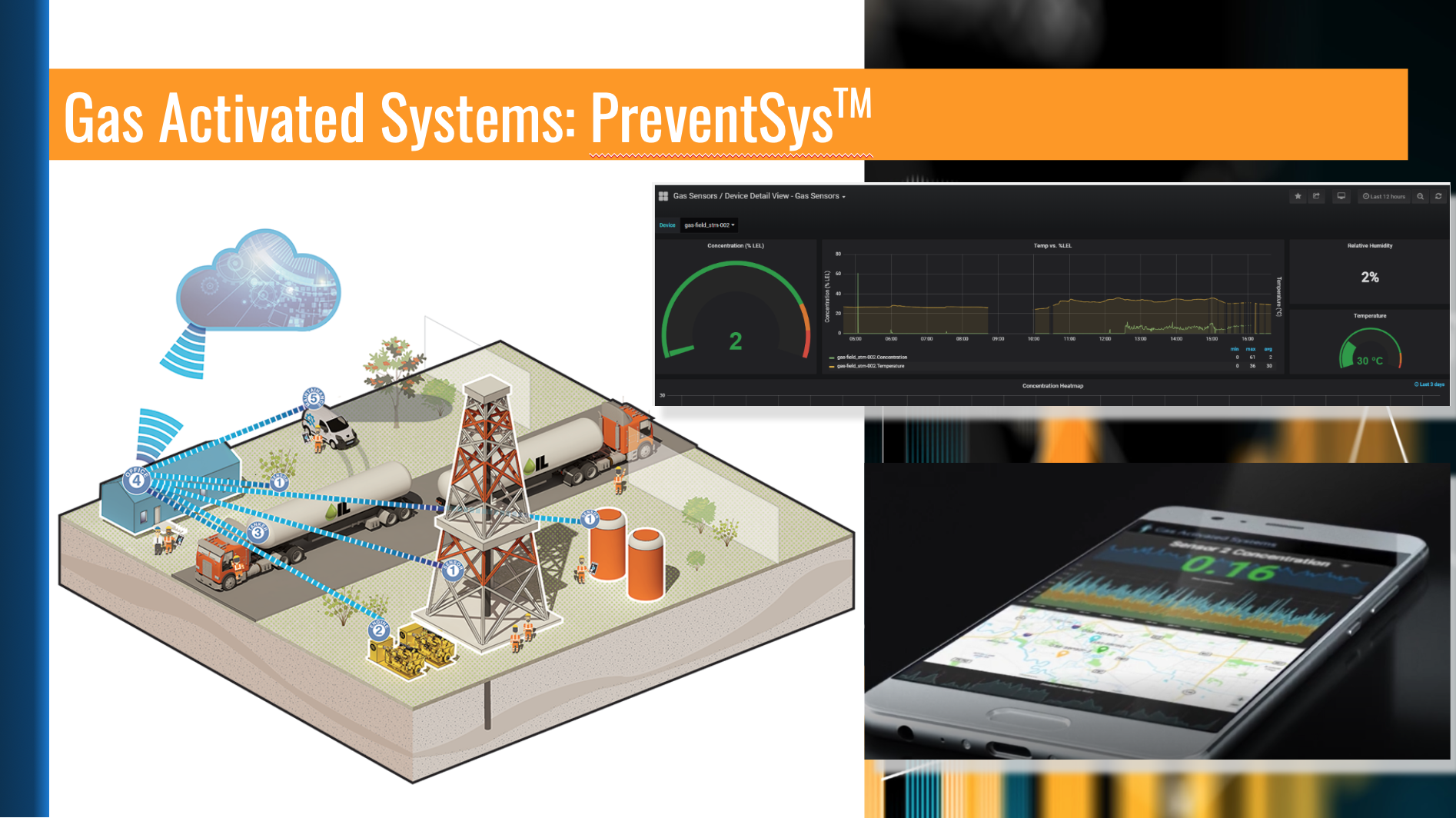
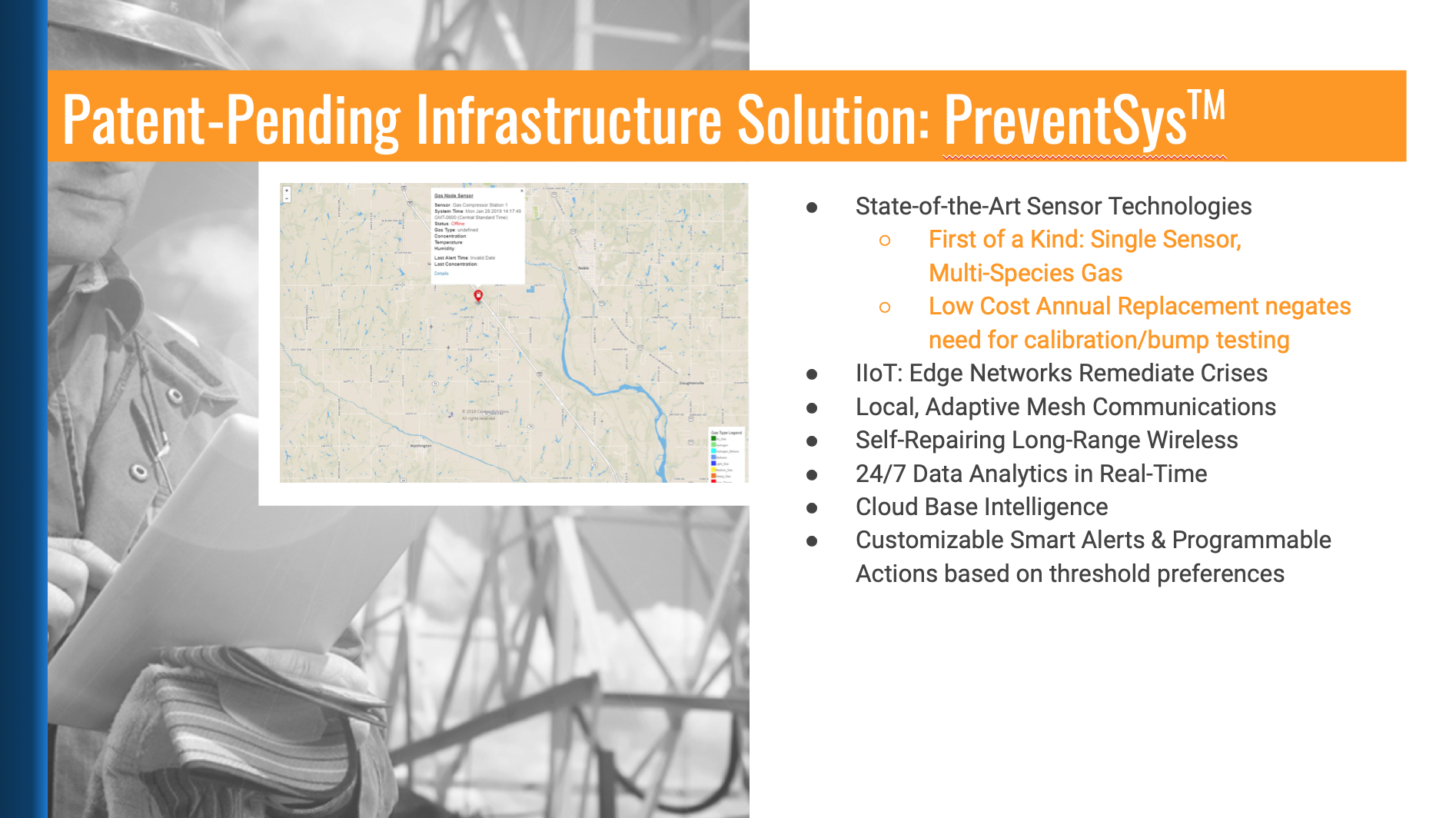
Use the specialized explosive gas monitoring systems on engine air intake
- Monitor air stream into engine for explosive gases.
- Detect for dangerous concentration of gas by species.
- Multi-method engine shutdown before problem develops.
This is a fundamental change in methods – detecting for explosive gases before the overspeed event occurs rather than waiting until the event begins to unfold.
GAS ActivatorSys™ is a GasSys sensor plus engine shutoff valve system. While directing the air intake shutoff to protect the asset to which it is assigned, it reports into the array of sensors throughout the field into PreventSys to provide wide area engine overspeed protection. ActivatorSys detects and identifies a multitude of explosive gases. Appropriate action is directed based on gas species, concentration, location, rate of increase, and other relevant qualities. This patent-pending, fully-integrated component is capable of not only preventing an engine runaway on the unit detecting the suspect vapor, but, can also communicate and direct the actions of other assets and personnel within the facility through the PreventSys platform.
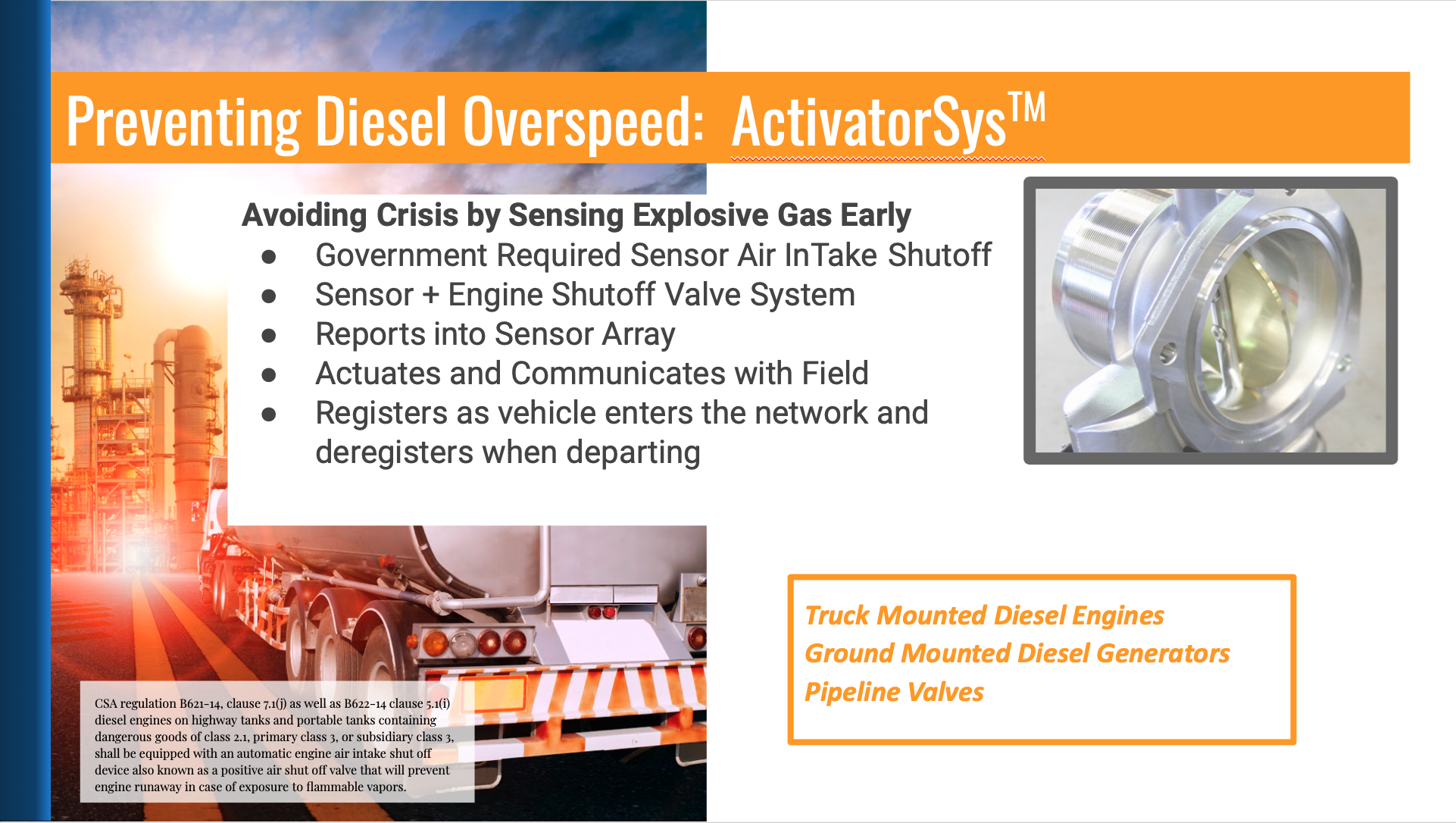